LEV Inspection Newport: A Guide to Compliance and Safety for Your Business
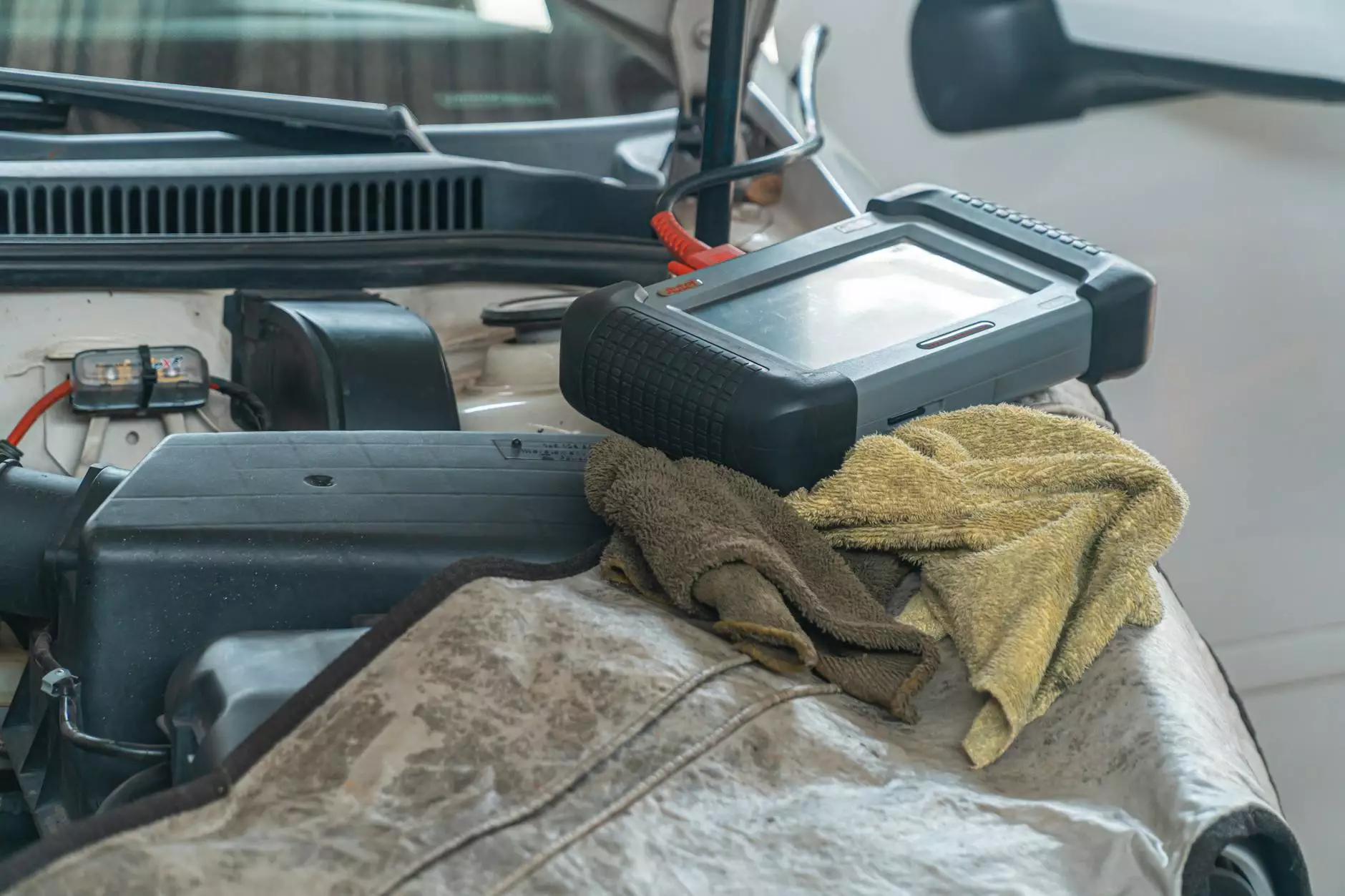
In today's rapidly evolving business environment, safety and compliance are paramount. This is particularly true when it comes to workplaces that involve industrial processes generating hazardous substances. A crucial element in ensuring a safe working environment is the Local Exhaust Ventilation (LEV) system. This article explores the significance of LEV Inspection in Newport, focusing on its benefits, compliance requirements, and how businesses can effectively implement these practices.
What is Local Exhaust Ventilation (LEV)?
Local Exhaust Ventilation is a system designed to control exposure to airborne contaminants. These can arise from a variety of sources, including dust, fumes, vapours, or mists during industrial processes. The primary function of LEV systems is to capture these hazardous substances at their source, preventing them from dispersing into the wider work environment.
The Importance of LEV Inspection in Newport
For businesses operating in sectors such as Home & Garden, conducting regular LEV inspections is not just a regulatory requirement; it's a fundamental part of maintaining a healthy workplace. Here are several reasons why LEV inspections are critical:
- Health and Safety Compliance: Under the Health and Safety at Work Act and the Control of Substances Hazardous to Health (COSHH) Regulations, employers are legally obligated to minimize employee exposure to hazardous substances.
- Preventing Health Risks: Continuous exposure to harmful airborne contaminants can lead to severe health issues, including respiratory diseases and long-term health complications.
- Improving Employee Well-being: A safe working environment boosts employee morale and productivity. Employees are more focused and effective when they feel secure at work.
- Reducing Liability: Regular inspections mitigate the risk of accidents and legal issues, protecting your business from potential lawsuits and compensation claims.
- Enhancing Productivity: Efficient LEV systems contribute to a clean and pleasant working environment, which can lead to enhanced operational efficiency.
When Should Your LEV System Be Inspected?
For effective management of LEV systems, it is essential to establish a robust inspection schedule. Regulations recommend that LEV systems should be thoroughly inspected:
- At least once every 14 months
- Whenever there are significant changes to the system or the processes it serves
- After any maintenance or modifications to the LEV equipment
By adhering to this schedule, businesses not only ensure compliance with legal requirements but also maintain high standards of air quality and safety.
Conducting a Thorough LEV Inspection
A complete LEV inspection involves several key steps to assess the efficiency and functionality of the system. Here’s a detailed breakdown of what to expect during an LEV inspection:
1. Visual Inspection
The inspector will begin with a thorough visual examination of the LEV system, checking for any physical damages, corrosion, or signs of wear. This includes the ductwork, hoods, fans, and filters, all of which play vital roles in the efficiency of the system.
2. Performance Testing
Following the visual inspection, performance testing is conducted. This may involve measuring the airflow in different parts of the system to ensure it is operating within acceptable limits. Tools such as anemometers may be used to capture accurate data relating to air velocity and airflow rates.
3. Maintenance Review
The inspector will also review the maintenance history of the LEV system. This includes checking that regular servicing is being undertaken and that any previous issues have been effectively resolved.
4. Employee Consultation
Part of an effective inspection involves speaking with employees who operate near the LEV system. Understanding their experiences and concerns provides valuable insight into the system's performance and any potential issues that are not easily observed.
Choosing the Right LEV Inspection Service in Newport
When selecting a service provider for LEV Inspection in Newport, it is crucial to choose a company with a strong track record and compliance expertise. Here are some tips to ensure you make the right choice:
- Check Qualifications: Ensure the inspectors are certified and have the necessary qualifications to carry out LEV inspections as per the regulations.
- Experience Matters: Opt for a service provider with a proven history of conducting LEV inspections in your industry, particularly within the Home & Garden sector.
- Look for Comprehensive Services: Your selected provider should offer a range of services, including inspection, maintenance, and system design, to ensure the longevity and efficiency of your LEV system.
- Read Reviews: Look for testimonials and reviews from previous clients to gauge their reputation and reliability.
Benefits of Regular LEV Inspection
The advantages of prioritizing LEV inspections cannot be overstated. Below are some key benefits:
1. Regulatory Compliance
Meeting legal obligations is a primary benefit of regular inspections. Compliance prevents legal repercussions and fosters a culture of accountability within the organization.
2. Cost Efficiency
While there may be costs associated with inspections, the long-term savings from preventing health-related claims and potential fines for non-compliance are significant. Investing in LEV systems also prolongs their lifespan, reducing overall maintenance costs.
3. Peace of Mind
Knowing that your working environment is safe leads to peace of mind for both employers and employees. This positive atmosphere can enhance teamwork and productivity across the board.
4. Continuous Improvement
Regular inspections create opportunities for continuous improvement. Businesses can adapt and optimize their LEV systems based on evolving standards, technologies, and employee feedback.
Case Study: LEV Inspection Success in Newport
To illustrate the impact of effective LEV inspections, let’s consider a hypothetical case study of a gardening supplies manufacturer based in Newport. This company faced numerous challenges, including complaints about poor air quality and a rise in respiratory ailments among employees.
Upon conducting a comprehensive LEV inspection, the following issues were identified:
- Inadequate airflow in certain processing areas
- Improperly maintained filters leading to decreased efficiency
- Lack of employee awareness about the importance of using LEV systems
Following the inspection results, the company implemented a series of corrective actions, including upgrading existing LEV systems, instituting an employee training program, and scheduling regular maintenance and inspections. The outcome was remarkable: employee health improved, complaint rates dropped significantly, and the overall productivity of the workforce saw a notable increase.
Conclusion
In conclusion, prioritizing LEV Inspection in Newport is essential for businesses in the Home & Garden sector, ensuring compliance, safeguarding employee health, and enhancing productivity. By understanding the importance of LEV systems and committing to regular inspections, businesses can create safer work environments that foster long-term success.
Ready to schedule a LEV inspection for your business? Contact Safe Plant UK today at safeplantuk.co.uk and take the first step towards ensuring a safer, healthier workplace!
lev inspection newport